To put Six Sigma in perspective, we started by discussing the beginning of Six Sigma in the 1980s and then its antecedents from the early twentieth century to the recent history of TQM.
JIT and lean. The Six Sigma of the late 1980s and early 1990s- the first generation-was part of continuous improvement or total quality efforts often became islands of isolated change that died when unsupported by the business leadership. What can be called the second generation of Six Sigma can be fairly said to have first emerged at AlliedSignal in 1994, where it was led by CEO Larry Bossidy. Hall marks of the second generation are that Six Sigma is part of the corporate business plan and is key to achieving business objectives, with top leadership support and often intimate involvement. Another key to difference from the first generation is that the second generation of Six Sigma starts with the Voice of the Customer. In its first generation, Six Sigma process improvement methodology included four logically linked phases, measure-analyze-improve-control. In the second generation, during the GE Capital deployment in 1995, a new first phase, define, was added, becoming the DMAIC methodology now used in most Six Sigma Implementations. In the Define phase, data DMAIC methodology now used in most Six Sigma Implementations. In the benne pridse, dadd is used to verify customer needs and requirements and to identify the Critical-to-Quality characteristics for customers satisfaction. Thus. Six Sigma has the potential to create processes with maximum efficiency and effectiveness. And by integrating process improvement (DMAIC). process, product and service Design(ie. Design for Six Sigma, or DESS), and process management into a comprehensive approach to implementing business strategy. Six Sigma finally evolved into a program that could be used to drive the business instead of marrow focusing on quality.
In the May 2002 issue of Six Sigma Forum, Matt Barney Of Motorola tells how the second generation of Six Sigma differs from the first generation at the place of Six Sigma’s birth.
While Six Sigma was originally created as a continuous quality improvement technique, today it is significantly different than the Total Quality Management (TQM) approach of the 1980s 9Here are) the key differences between Six Sigma and TOM .
SIX SIGMA | TOTAL QUALITY |
EXECUTIVE OWNERSHIP | SELF – DIRECTOR WORK TEAMS |
BUSINESS STRATEGY EXECUTION SYSTEM | QUALITY INITIATIVE |
TRULY CROSS FUNCTIONAL | LARGELY WITHIN A SINGLE FUNCTION |
FOCUSED TRAINING WITH VERIFIABLE RETURN | MO MASS TRAINING IN STATISTICS & QUALITY |
BUSINESS RESULTS ORIENTED | RETURN ON INVESTMENT QUALITY ORIENTED |
Six Sigma. A Critical Difference. No less an authority than Dr. Joseph M. Juran has said that while he does not see any significant advances in six Sigma. he does think it has succeeded in gaining the participation and commitment of top leadership, a critical success factor that every other process improvement program failed to achieve, with a few notable exceptions.
such as Motorola under Bob Calvin’s legendary Leadership.
Evolution to a Revolution. What makes Six Sigma so attractive is that it integrates a great deal of what we have learned about getting sustainable results in manufacturing and services. But in seeing Six Sigma as a part of that evolution, it would be a mistake to think of Six Sigma as about evolutionary, incremental improvement. From the stretch performance targets sell for Six Sigma projects to transforming the mind-sets of the current generation and next generation of leaders through block belt and Master Black Belt training and successful projects, Six Sigma is about big paybacks and big impacts on culture and leadership
LEVERAGING PROCESSES, PEOPLE, CUSTOMERS, AND CULTURE
The world is concluding that the way to become a world-class company if to create superior process performance, as that is what ensures superior products and services for customers Superior process performance maximizes value for the customer and the shareholder. The beauty of Six Sigma is that it can be applied again and again to improve processes or to design new processes that continuously align the company with changing customer needs and
wants.
Change is always difficult, established organizational structures and expert functional areas are resistant. To change the way work done in the hierarchical structures that are today’s corporations, leaders need to drive the effort. And advantage of Six Sigma is that it requires leaders to be actively engaged in leading the pursuit of customer satisfaction. Also the idea of process improvement through the human factor in change at both the leadership and the process levels. The people who work in the process become the change agents using the Six Sigma tool kit. Changing processes changes behavior. However, changes in culture the “Collection of covert rules, values and principles that are enduring and guide organizational behaviour” can only be aligned with strategy and leader behaviour.
Here are some ways in which leaders reinforce the kind of culture and organization they wish to create.
• By what they pay attention to, measure, and control
• By their reaction to critical issues in the organisation
• By the way they model the role, teach, and coach
• By their criteria for rewards, promotion, and hiring
• By the question they ask
WHERE IS SIX SIGMA GOING?
Process centered organisation delivering products and services that meet or exceed customer expectations call for new management paradigms and new leadership skills. Becoming a six sigma company versus a company doing Six Sigma, as ken freeman of Quest Diagnostics puts it, is journey of risk and challenge, but the risk can be offset and the challenges met by two unique aspects of Six Sigma. its ability to develop change leadership skills and its unrelenting focus on satisfying the customer.
Six Sigma helps leaders define the future, the kind work people will do, the skills that are needed, the ways performance will be measured and rewarded, the careers of the future, the role managers will play. and how strategy will be executed.
Results are achieved through people. With Six Sigma, work and the people who do it are refocused from tasks to processes. Six Sigma gives everyone in the organization a common language and set of tools for achieving what is valuable to the customer. Scientific management applied to employee doing is replaced with the scientific method being practiced by every employee working in a process.
What is Six Sigma is Not
Six Sigma is not another quality program. That’s an important point to emphasise.
Business exists for one purpose- to profitably serve customers. So it follows that any problem-solving initiative should do the same, Six Sigma uses your resources to fix identifiable, chronic problems, it proves its value by connecting outcomes to your bottom
line.
Quality programs lay a valuable foundation in creating a quality mindset. But ask yourself if any you’ve experienced have generated specific financial results like Six Sigma. It’s very possible youl’ll answer, “No,” since a primary criterion for selecting six sigma projects is to return money to your balance sheet as the results of full – time efforts by dedicated recourse. Six Sigma is not theory It’s practice of discovering the vital few processes that matter most It defines, measures, analyses, improves and controls them to tie quality improvement directly to bottom-line results.
Six Sigma is an active, involved effort that puts practical tools to work to root defects at all levels of your organization. It’s not a theoretical exercise. you don’t think about Six Sigma – you do it.
Since the success of Six Sigma is directly linked to monetary outcomes. it generates real-world results. It uses the most readily available resources in an organization – its human assets. That means that positive, tangible results consistently show up wherever and whenever people are engaged in implementing Six Sigma techniques.
Six Sigma is not a training program. Of Course, practitioners are trained in the methodology to ensure correct implementations and results. But Six Sigma is a Business strategy that fosters a cultural shift at all levels. Permeating departments, functional groups, and all levels of management, Six Sigma changes the outlook and practices of everyone in the organisation From workers on assembly lines and bookkeepers in accounting to operations managers and human resource personnel, training exists only to instill the method, facilitate transformation, and get financial results by attacking chronic defects with proven statistical tools,
Six Sigma Myths
There are many myths and misunderstanding about Six Sigma and as you participate in it. you’ll probably hear at least one of the following.
Six Sigma…
… Works only in manufacturing settings.
… Doesn’t include customer requirements … is repackage TQM.
… Uses difficult-to-understand statistics.
.. is an accounting game without real savings.
… is just training
… is a magic pill with little effort.
Just remember that Six Sigma actively links people, processes, and outcomes in a rigorous, adaptable way to get you the results you’re looking for. No matter the industry. business. product, or service, as you apply Six Sigma. you’ll see the tangible results on your projects.
Six Sigma projects can be devised to improve activities and processes in areas as.
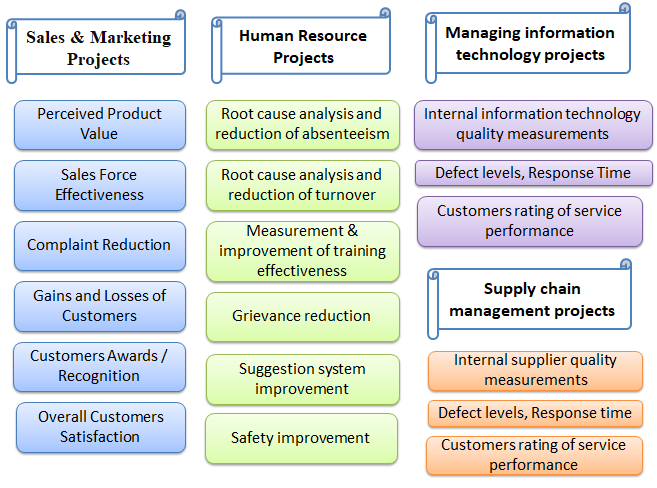